The single-stage single-suction vertical centrifugal pump is a fluid transfer device widely used in industrial, construction, and municipal applications. Its compact structure and ease of installation make it the preferred choice for scenarios with vertical space constraints. To ensure safe and stable operation, strict adherence to its operating conditions is essential. Below is a detailed analysis of the applicable environments and operational specifications for such pumps from multiple dimensions.
I. Medium Characteristics Requirements
Single-stage single-suction vertical centrifugal pumps have specific limitations on the physical properties of the conveyed medium.
- Temperature: The medium temperature must be maintained within -20°C to 120°C. Exceeding the upper limit accelerates seal aging, while temperatures below the lower limit risk medium freezing.
- Solid Content: Solid particles in the medium must not exceed 0.1% by volume, with particle diameters smaller than 0.2mm. High particle concentrations accelerate impeller wear and reduce pump lifespan.
- pH Value: The medium’s pH should remain between 6 and 8.5. For strongly acidic or alkaline media (e.g., hydrochloric acid), pumps with specialized materials—such as PTFE-lined or full stainless steel pump bodies—are required.
II. Pressure and Flow Parameters
- Inlet Pressure: Must be no less than 0.3MPa to prevent cavitation damage to the impeller.
- Outlet Pressure: Varies by model, with standard models typically capped at 1.6MPa. Real-time pressure monitoring via gauges is critical to ensure operation within the “green zone.”
- Flow Rate: Adjust flow within 70%–120% of the rated capacity. Prolonged overloading causes motor burnout, while underloading risks axial force imbalance. A frequency conversion device is recommended for precise flow control and energy efficiency optimization.
III. Environmental Adaptability
- Ambient Temperature: Maintain between -15°C and 40°C, with humidity below 90%. Outdoor installations require rain covers to prevent electrical component short circuits.
- Altitude: For installations above 1,000 meters, compensate for reduced atmospheric pressure to avoid performance degradation.
- Vibration Control: Baseplate vibration velocity must be below 2.8mm/s (RMS). Use vibration-damping pipe supports and, for high-power pumps, install independent concrete foundations weighing 1.5× the pump’s weight.
IV. Electrical Parameter Matching
- Voltage Fluctuation: Keep within ±5% of the rated voltage, with frequency deviation under ±1Hz. For three-phase motors, phase voltage imbalance must be <1%.
- Overload Protection: Install devices to cut power when current exceeds 15% of the rated value.
- Cabling: Use copper-core cables (cross-section ≥2.5mm²) for distances under 50m. For longer distances, verify voltage drop to ensure motor terminal voltage stays above 342V (in 380V systems).
V. Operation and Maintenance Protocols
- Pre-Startup: Prime the pump and vent air. Never allow dry running >30 seconds. Conduct a no-load test before initial operation, gradually ramping up to full load.
- Routine Checks: Monitor bearing temperature (≤75°C) and stuffing box leakage (≤60 drops/minute).
- Lubrication: Replace grease every 2,000 operating hours, filling bearings to 1/3–1/2 capacity with lithium-based grease.
- Mechanical Seals: Replace every 8,000–10,000 operating hours, using specialized tools to avoid shaft sleeve damage.
VI. Special Condition Handling
- High-Temperature Media: Implement a preheating process with a ≤30°C/h heating rate to prevent thermal stress.
- Crystallizing Media: Flush flow channels with water immediately after shutdown; consider adding insulation jackets.
- Intermittent Operation: Start the pump weekly for ≥30 minutes to prevent stagnation. For long-term storage, drain residual liquid, apply rust inhibitors to critical components, and seal flanges with plastic film.
Conclusion
Reliable operation of single-stage single-suction vertical centrifugal pumps depends on strict adherence to these conditions. Users should select models suited to actual working parameters, perform regular performance tests, and maintain detailed operation logs. A preventive maintenance system extends service life and reduces downtime. For specialized applications, consult manufacturers for customized designs to ensure optimal system-process alignment.
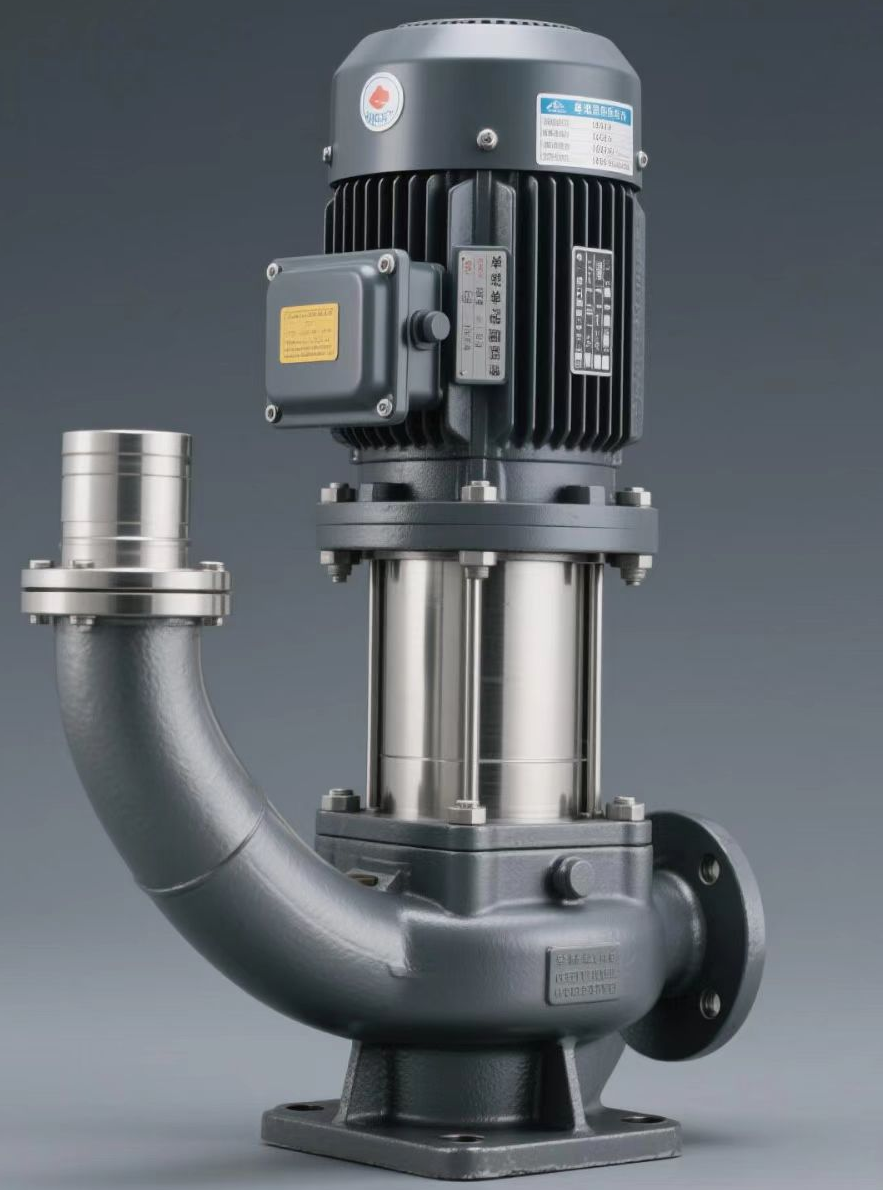